Common Electric Motor Problems and How to Fix Them
Electric motors are crucial components in many industrial and residential applications. However, they can develop issues over time that degrade performance. This article explores some of the most frequent electric motor problems and provides troubleshooting tips to diagnose and repair them.
Burning Smell and Overheating
Excessive heat is one of the most common electric motor faults. Possible causes include:
- Overloading - The motor is undersized for the connected load, causing overexertion.
- Poor Ventilation - Blocked cooling fans or vents prevent adequate airflow.
- Bearing Issues - Worn or stuck bearings generate friction and heat.
- Low Voltage - Motors running on insufficient voltage work harder to produce rated output.
Fixes involve inspecting and replacing worn parts, freeing blockages, and ensuring proper supply voltage. Reduce loads on overloaded units.
Another interesting products
Noise and Vibration
Clanking, grinding and shaking sensations during motor operation signal a problem. Likely reasons are:
- Unbalanced Rotors - Uneven mass distribution leads to vibration.
- Bearing Defects - Damaged or worn bearings allow shaft wobble.
- Misalignment - Improper installation or shifting leads to alignment issues.
- Loose Parts - Fasteners or motor components coming loose cause rattling.
Isolate the source of vibrations and noise by inspection. Rebalance or realign components. Replace any worn or damaged parts.
Similar products
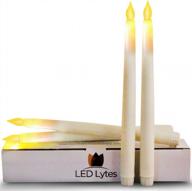
49 Review
Low Power and Torque
Sluggish performance and difficulty starting are signs of weak motor power. Check for:
- Poor Connections - Loose wiring leads to high resistance and power drops.
- Undervoltage - Lower than rated voltage reduces torque production.
- Incorrect Wiring - Wrong connections impact starting and running torque.
- Jammed Rotors - Mechanical seizing prevents proper rotation.
Verify sound connections, correct voltages and wiring. Remove jams and test windings for faults.
For continued motor reliability, schedule regular maintenance and promptly address any emerging issues before they worsen. Consult professionals for complex repairs.
Burning Smell and Overheating Issues in Electric Motors
Nothing grabs your attention faster than the acrid smell of burning insulation coming from an electric motor. Excessive heat is the enemy of motors and can quickly lead to complete failure. Rapid diagnosis and repair is crucial to get things running smoothly again.
Overloading
Connecting too much load for the motor's horsepower rating stresses the windings. For example, operating a 1 HP motor at a 2 HP load causes overheating. The motor draws excess current to produce enough torque, but this overloads the windings.
Check nameplates for the rated load and do not exceed it. A motor running too hot with an appropriate load may need to be replaced with a larger unit.
Poor Ventilation
Fans, fins and vents dissipate heat. Blockages make cooling ineffective. For example, dust buildup on a fan restricts airflow leading to overheating. Ensure proper clearance around ventilation openings and keep surfaces clean.
Bearing Issues
Worn, underlubricated or stuck bearings generate friction and heat. Warning signs include squealing noises, loose shafts and higher operating temperatures. Routinely lubricate bearings and replace worn components to prevent seizing.
Low Voltage
Motors designed for 230V drawing 180V work harder trying to produce rated power. The extra current creates heat which damages insulation over time. Verify incoming voltage is within 10% of motor rating. Consider buck-boost transformers to regulate voltage.
Other common reasons for overheating like unbalanced voltages, shaft misalignment and high ambient temperatures also require attention. Listen for unusual sounds, monitor temperatures and be alert to smells to catch problems early. Adequate cooling and preventive maintenance keeps motors running efficiently.
Troubleshooting Noise and Vibration in Electric Motors
Electric motors naturally produce some level of noise and vibration during operation. However, excessive levels can indicate developing problems. Isolating the causes and rectifying them promptly prevents more extensive damage.
Unbalanced Rotors
The rotor consists of conductors wound around a shaft. Uneven mass distribution due to manufacturing defects or damage can cause imbalance. This imbalance generates strong vibrations. Rebalance the rotor if possible, or replace it if damage is too severe.
Bearing Defects
Ball bearings allow smooth shaft rotation. With prolonged use, wear, pitting or fatigue damage can occur. This leads to looseness between balls and races. The resulting wobble creates noise and vibrations. Inspect bearings regularly and replace worn ones.
Top products in 🚗 Electric Motors
Misalignment
Motors must be properly aligned with connected loads. Misalignment puts radial and axial loads on shafts. This strains components leading to rattling vibrations. Laser alignment tools can diagnose and correct shaft misalignment.
Loose Parts
The stator core consists of stacked laminations. Over time lamination adhesion degrades, causing them to rattle when energized. Fasteners securing end bells and fans can also work loose. Check and tighten all hardware periodically.
Unbalanced Supply
Each phase must have equal voltage. Unbalanced voltages cause uneven magnetic forces and vibration. Check supply voltage to all terminals with a multimeter. Rectify unbalances with buck-boost transformers.
Regular maintenance like lubricating bearings, checking fastener tightness, and monitoring vibration can identify problems early. Correct alignment ensures smooth power transmission. Promptly replacing worn parts minimizes collateral damage and extends motor life.
Low Power and Torque Problems in Electric Motors
Lackluster performance from an electric motor indicated by slow acceleration, inability to start loads, or low running speed usually stems from low power and torque output. Identifying the root causes quickly helps get things back up to speed.
Poor Connections
Loose terminal connections have higher resistance than tight ones. This causes voltage drops before the motor windings, reducing available power. For example, a loose supply wire may drop 6 volts, leaving the motor underpowered.
Check all wires are securely fastened. Tighten terminal screws to the specified torque. Ensure lugs make solid contact with bars.
Undervoltage
Motors are designed for a certain voltage rating. Undervoltage operation hampers performance. A 230V motor supplied with 200V struggles to produce its full rated torque and power.
Verify incoming voltage is within 10% of motor rating. Consider buck-boost transformers to regulate voltage.
Incorrect Wiring
Wrong phase sequencing scrambles the current flow in windings, affecting starting and running torque. For example, swapping any two line leads creates reverse rotation issues.
Ensure correct wire colors match supply phases. Follow manufacturer diagrams for making connections.
Jammed Rotors
Mechanical seizing due to stuck bearings or bent shafts prevents free rotation. This hampers the motor’s ability to reach operating speed and generate torque.
Isolate the jam and clear it. Replace damaged components like bearings. Check rotor-stator gap.
Early detection of developing problems based on performance changes gives the best chance for quick repair. Schedule periodic maintenance and testing.
Replacing Brushes and Bearings in Electric Motors
Brushes and bearings are critical components that wear out over time. Replacing them properly maintains motor performance and extends service life.
Brushes
Brushes conduct current to the spinning armature in a DC motor. But the friction gradually wears down the carbon blocks requiring periodic replacement. Signs include noisy operation, sparking and reduced speed.
Use a brush gauging tool to measure how much length remains. Generally replace brushes when they reach half their original size. Record brush dimensions when new as a baseline.
Disconnect power supply and remove brush caps. Lift brushes just enough to disconnect pigtails. Slide new brushes in place oriented correctly. Reconnect pigtails and secure caps.
Bearings
Bearings allow the shaft and rotor to spin freely. But contaminants, moisture and wear degrade them over time. Symptoms include vibrations, noise and loose shafts.
Inspect bearings regularly for visible damage. Use a dial indicator to check for play indicating wear. End play over 0.001 inches merits replacement.
Follow manufacturer guidance for pulling old bearings and pressing in new ones. Ensure proper fit and check for free rotation. Lubricate before reassembly.
Brushes and bearings are inexpensive components that keep motors running right. Replace them proactively to prevent unplanned downtime. Use quality parts that meet OEM specifications.
Electric Motor Safety Concerns and Proper Usage
Electric motors can pose serious hazards if not operated and maintained properly. Being aware of the risks and following safe practices prevents accidents and injuries.
Electrical Hazards
Motors contain high voltage electricity. Accidental contact can result in shocks, burns or electrocution. Never open enclosures while energized. Use proper PPE when servicing.
Ensure adequate overload and short circuit protection. Size conductors and ratings for the motor current draw. Keep connections tight to prevent arcing.
Follow lock-out tag-out procedures during maintenance. Check for residual voltage before starting work.
Moving Parts
Rotating components like shafts, couplings and fans can catch on clothes, hair or tools leading to entanglement injuries. Keep guards in place and tie back long hair.
Don't wear loose fitting clothing and jewelry when working around motors. Remove tools immediately after completing adjustments or repairs.
Noise
Electric motors generate high noise levels that can cause hearing damage over time. Use appropriate ear protection when working around them. Keep inspection doors closed.
Minimize exposure time in noisy environments. Isolate particularly loud motors using enclosures or separate rooms.
Following safety guidelines, using protective equipment and regular maintenance keeps things running safely. Consult experts for anything unclear.
Choosing the Right Electric Motor for Your Application
Selecting the optimal motor for an application requires matching technical specifications to operating requirements. Consider these key factors:
Motor Size
The motor must be sized appropriately for the connected load to avoid overworking or underutilizing it. Oversize motors run inefficiently while undersized ones overheat or burn out prematurely. Refer to load equipment nameplates for horsepower ratings.
Duty Type
Determine if operation is continuous or intermittent. Motors in conveyors run continuously, while those in machine tools only run intermittently. Specify motors for either constant or variable duty cycles.
Speed and Torque
Torque requirements dictate motor selection. For example, positive displacement pumps need high starting torque but lower running torque. Choose motors with speed-torque curves matched to the driven load.
Environment
Hazardous location motors certified for use in explosive or wet environments are required for such conditions. General purpose TEFC motors suit clean, dry locations.
Enclosure Type
Open drip-proof motors vent heat better but admit contaminants. Totally enclosed or sealed units protect internal parts in dirty or outdoor settings.
Consult manufacturers to select the optimal motor design, winding, and construction for an application. Proper sizing and specification prevents problems down the line.
What Are The Most Common Problems Faced By Users Of Electric Motors??
Based on the search results, here are the 10 most common problems faced by users of electric motors:
- Overheating and high temperatures
- Power surges
- Bearing wear and damage
- Exposure to moisture and contamination
- Low resistance
- Electrical overload
- Vibration
- Accumulation of dust and debris
- Winding insulation breakdown
- Voltage imbalance
These problems can lead to motor failure, which can result in costly downtime and repairs. It is important to understand the common problems that can occur with electric motors and take measures to prevent them from happening. Regular maintenance and proper care can help prevent total motor failure.
What Is The Most Common Cause Of Electric Motor Failure?
According to the search results, winding insulation breakdown and bearing wear are the two most common causes of electric motor failure. However, these conditions can arise due to many different reasons. Here are some of the most common causes of electric motor failure:
- Overheating and high temperatures
- Dirt and contaminants
- Overcurrent or electrical overload
- Moisture and exposure to water
- Low resistance due to insulation breakdown, corrosion, or physical damage
- Misalignment of the motor shaft
- Vibration and physical damage
- Power surges and voltage imbalances
It is important to understand the common causes of electric motor failure to prevent costly downtime and repairs. Regular maintenance and proper care can help prevent these issues from occurring.