Move Heavy Objects with Ease
Moving heavy objects in warehouses, factories, construction sites or other industrial settings can be a challenging task. However, with the right equipment and techniques, it doesn't have to be back-breaking work. There are various material handling solutions that can help you safely and efficiently transport large, bulky items.
Forklifts
One of the most common pieces of equipment for heavy lifting is the forklift. Forklifts use two prongs, or "forks", to lift objects from underneath. They can handle loads ranging from a few hundred pounds to several tons. Here are some tips for using forklifts:
- Choose the right forklift capacity for the loads you need to lift
- Keep the load balanced on the forks and watch for shifting
- Drive slowly, especially when turning or on uneven ground
- Lift loads only a few inches off the ground when transporting
- Never stand under raised forks, even when empty
Pallet Jacks
Pallet jacks, also known as pallet trucks, are designed to move pallets of goods. They utilize a set of forks and wheels to lift and roll loaded pallets. Pallet jacks are smaller in capacity than forklifts but offer maneuverability in tight spaces. Tips for pallet jack use include:
- Make sure the pallet is in good condition before lifting
- Keep feet clear when pumping the jack to raise the load
- Push the load slowly and cautiously
- Avoid abrupt stops or turns
- Lower the pallet completely when parking the jack
Equipment | Capacity | Key Features |
---|---|---|
Forklift | 2,000 - 70,000 lbs | Powerful lifting capacity, handles very heavy loads |
Pallet Jack | 5,000 - 10,000 lbs | Maneuverable, used for pallets of goods |
Final Tips
Safety should always be the top priority when moving heavy objects. Ensure equipment is properly maintained and operators are trained. Use appropriate rigging hardware when lifting irregular or awkward loads. Taking the proper precautions makes transporting bulky, heavy materials as easy as possible.
Transport Goods Quickly and Safely
Moving materials efficiently through a facility or work site is crucial for operations. However, safety should never be sacrificed for speed when transporting goods. The right equipment and procedures can help you swiftly move loads without accidents.
Conveyor Systems
Conveyors are automated material handling equipment that transports items from one point to another. They provide consistent, rapid throughput of goods. Types of conveyors include:
- Belt conveyors - Use a rubber or fabric belt stretched over pulleys to move objects.
- Roller conveyors - Use gravity and rolls to convey cartons or packages.
- Overhead conveyors - Transport materials suspended from overhead tracks.
Ensure conveyors have protective guards and emergency shut-off switches. Only trained staff should operate or service conveyors.
Automatic Guided Vehicles
AGVs are self-guided transport vehicles that follow programmed routes around facilities. They are often used to:
- Move raw materials to production lines
- Transport finished goods to loading docks
- Deliver components to assembly stations
AGVs increase efficiency and do not require human operators. Safety features such as scanners, cameras and warning alarms are critical.
Transport Method | Speed | Safety Considerations |
---|---|---|
Conveyors | High throughput | Guards, emergency stops |
AGVs | Swift automation | Warning systems, programmed routes |
Final Tips
Creating a safe traffic plan and having trained staff monitor operations are key for safe, speedy transport. Also ensure goods are properly packaged, loaded and secured. With the right precautions, you can achieve fast material movement without incident.
Streamline Warehousing Operations
Warehouses and distribution centers are hubs of constant activity. Managing inventory, storage and order fulfillment efficiently is key. There are various strategies and material handling solutions that can optimize workflows and reduce costs.
Warehouse Management Systems
A WMS is a software solution that helps track inventory and coordinate activities. Features include:
- Inventory management - Monitor stock levels and product locations.
- Order processing - Streamline picking, packing and shipping.
- Task management - Assign and track worker tasks like put-away or replenishment.
- Reporting - Generate data on performance metrics.
An effective WMS improves accuracy, productivity and labor utilization in the warehouse.
Automated Storage and Retrieval
AS/RS systems use automated cranes and shuttles to store and retrieve inventory. Major benefits include:
- Increased throughput and faster order fulfillment.
- Maximized storage density using vertical space.
- Reduced labor requirements for put-away and picking.
- Higher accuracy than manual methods.
AS/RS streamlines operations 24/7 with precision.
Solution | Benefits |
---|---|
WMS | Enhanced inventory and order management |
AS/RS | Automated storage and retrieval |
Final Tips
Improving workflows through optimized layouts, 5S, and standardized processes brings further operational gains. Partnering with an experienced material handling integrator helps design the most efficient warehouse solutions.
Top products in 🚚 Material Handling
Lift Materials to New Heights
Elevating heavy or oversized loads safely is vital in many worksites. Whether loading cargo into trucks, stocking warehouse shelves or hoisting equipment for construction, specialized lifting equipment gets the job done.
Boom Lifts
Boom lifts provide temporary aerial access for working at height. Types include:
- Articulating booms - Extend horizontally and vertically for maximum reach.
- Telescopic booms - Extend vertically with multiple overlapping sections.
- Scissor lifts - Lift straight up without reaching over obstacles.
Proper operator training and fall prevention systems are essential for safety.
Gantry Cranes
Gantry cranes are fixed overhead crane structures that span working areas. They use hoists on trolleys to pick and place loads. Benefits include:
- Ability to handle very heavy loads.
- High height capability.
- Large coverage area for flexibility.
- Efficiency through electric power versus manual labor.
Precise control systems allow smooth, precise crane movements.
Equipment | Reach | Capacity |
---|---|---|
Boom Lifts | Up to 60 ft horizontally | Up to 1,000 lbs |
Gantry Cranes | Up to 150 ft span | Up to 50 tons |
Final Tips
Frequent inspections, load testing, and qualified operators are vital for overhead lifting equipment safety. Anti-drop and overload protections provide further control. Proper lifting equipment gives you the height and power to tackle tough elevation jobs.
Similar products
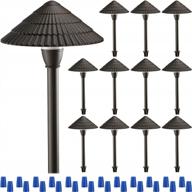
47 Review
How Material Handling Equipment Can Improve Your Business?
Material handling equipment can improve your business in several ways, including:
- Increased productivity and workflow: Material handling equipment can help your employees transport, locate, and pick inventory, allowing them to be more competent and productive with other tasks.
- Reduced operational costs: An effective material handling system allows your company to have the necessary stock in smaller spaces where possible, reduce time spent on internal operations, control inventory in real-time, reduce operational costs, and optimize the overall flow of goods in your facility.
- Improved employee satisfaction: By utilizing materials handling systems, employees are released from labor-intensive and monotonous tasks that will help them reduce stress levels and achieve overall satisfaction with work.
- Improved customer service: Material handling systems can help streamline workflow, reduce inventory excesses, shorten delivery times, and ultimately improve customer service.
How Can Material Handling Equipment Improve Safety In The Workplace?
Material handling equipment can improve safety in the workplace by:
- Minimizing manual handling risks: Manual material handling tasks such as lifting, carrying, and pushing can pose risks to employees. By utilizing material handling equipment, these tasks can be automated or made easier, reducing the risk of injuries.
- Providing protective equipment: Material handling equipment goes hand in hand with providing employees with proper protective gear such as eye protection, helmets, gloves, steel-toed safety boots, and guards to protect against impact or compression. This equipment helps minimize injuries when moving materials manually.
- Reducing workplace accidents: Implementing material handling systems can help prevent workplace accidents by reducing the need for labor-intensive and monotonous tasks. Employees can focus on more pressing tasks, reducing stress levels and improving overall satisfaction with work.
- Increasing productivity and efficiency: Material handling equipment allows employees to transport, locate, and pick inventory more efficiently. By automating or streamlining these processes, employees can be more competent and productive with other tasks, reducing the risk of errors and accidents.
Remember, it is important to follow proper work practices, equipment guidelines, and controls to ensure the safe handling and storage of materials.
What Are Some Examples Of Material Handling Equipment That Can Improve Workplace Safety?
Material handling equipment can improve safety in the workplace by:
- Minimizing manual handling risks: Manual material handling tasks such as lifting, carrying, and pushing can pose risks to employees. By utilizing material handling equipment, these tasks can be automated or made easier, reducing the risk of injuries.
- Providing protective equipment: Material handling equipment goes hand in hand with providing employees with proper protective gear such as eye protection, helmets, gloves, steel-toed safety boots, and guards to protect against impact or compression. This equipment helps minimize injuries when moving materials manually.
- Reducing workplace accidents: Implementing material handling systems can help prevent workplace accidents by reducing the need for labor-intensive and monotonous tasks. Employees can focus on more pressing tasks, reducing stress levels and improving overall satisfaction with work.
- Increasing productivity and efficiency: Material handling equipment allows employees to transport, locate, and pick inventory more efficiently. By automating or streamlining these processes, employees can be more competent and productive with other tasks, reducing the risk of errors and accidents.
Remember, it is important to follow proper work practices, equipment guidelines, and controls to ensure the safe handling and storage of materials.
What Are Some Examples Of Material Handling Equipment That Can Improve Workplace Safety?
There are several examples of material handling equipment that can improve workplace safety, including:
- Conveyors: Conveyors can help move materials from one location to another, reducing the need for manual handling and minimizing the risk of injuries.
- Forklifts: Forklifts are commonly used in warehouses and manufacturing facilities to move heavy loads. They can help reduce the risk of manual handling injuries and improve efficiency.
- Pallet jacks: Pallet jacks are used to move pallets of materials around the workplace. They can help reduce the risk of manual handling injuries and improve efficiency.
- Protective equipment: Protective equipment such as gloves, helmets, steel-toed safety boots, and eye protection can help minimize injuries when moving materials manually.
- Automated storage and retrieval systems: These systems can help reduce the need for manual handling and improve efficiency by automating the storage and retrieval of materials.
Remember, it is important to follow proper work practices, equipment guidelines, and controls to ensure the safe handling and storage of materials.