Pumps: The Heartbeat of Fluid Handling Systems
Pumps are essential components in a wide variety of fluid handling systems. From moving water and chemicals through industrial processes, to circulating heat transfer fluids through HVAC systems, pumps provide the motive force to get fluids from point A to point B.
Having the right pump for the job is crucial. Choosing the wrong pump can lead to poor system performance, frequent breakdowns, and increased operating costs. That's why taking the time to properly select and size pumps and accessories for your particular application pays dividends in the long run.
Understand the Liquid Properties
The first step is understanding the properties of the liquid you need to move. Important parameters include:
- Flow rate
- Viscosity
- Specific gravity
- Temperature
- Abrasiveness
- Corrosiveness
Knowing details like the flow rate range, liquid viscosity, and whether particles are present allows correct pump sizing and material selection.
Consider the System Parameters
You also need to look at the broader system design parameters, including:
- Suction and discharge piping configuration
- Elevation differences (static head)
- Operating pressure requirements
- Prime condition (flooded suction or lift)
This data is crucial for proper pump selection to match the system resistance (head) requirements.
Selecting the Right Pump
With liquid properties and system parameters defined, pump selection centers on choosing the proper pump style, materials, size, and features.
Work with a supplier to match the pump capabilities with your requirements. Small differences in hydraulics, construction, and component features can make big differences in performance, maintenance, and operating cost.
Taking the time up front to get the right pump will keep your fluid handling systems running reliably for years to come.
Choosing the Optimal Pump Style for the Job
With the wide variety of pump styles available, it can be daunting to select the right one for your fluid handling application. However, by carefully considering the liquid properties and system parameters, you can zero in on the optimal pump type.
Centrifugal Pumps
Centrifugal pumps are versatile and common. They use an impeller to accelerate liquid and convert velocity to pressure. Best for clean, low-viscosity fluids like water and light oils.
- Typically best efficiency at higher flows/lower pressures
- Handle thin liquids with little to no solids
- Often used for water, oils, solvents, and chemicals
Positive Displacement Pumps
Positive displacement pumps mechanically trap fluid and force it out the discharge. Good for high pressure or thick liquids.
- Generate high pressures even at low flows
- Good for high viscosity liquids like heavy oils and asphalt
- Used for pumping concrete, pastes, sludge, and more
Specialty Pumps
Unique pump designs for specialized applications:
- Drum and barrel pumps for lifting from containers
- Diaphragm pumps for abrasives and solids handling
- Peristaltic pumps for gentle, sterile pumping
- Magnetic drive pumps for zero-leakage hazardous fluids
Let the Application Guide Selection
There is overlap between pump types, but the fluid properties and system conditions will generally point you toward an optimal choice. Don't just default to a centrifugal - take the time to make sure the pump style suits the liquids and parameters involved.
Discuss your specific needs with an application engineer to dial-in the right pump selection.
Comparing Major Pump Types
When selecting a pump, the three main styles to choose from are centrifugal, positive displacement, and specialty pumps. Each has pros and cons to consider.
Centrifugal Pumps
- Operate by accelerating liquid with an impeller, converting velocity to pressure
- Simple, versatile, and generally low maintenance
- Best efficiency typically at higher flows and lower pressures
- Handles clean, thin, low-viscosity fluids like water, oils, solvents, etc.
- Often used for water supply, circulation, boosting, and transfer duties
Positive Displacement Pumps
- Trap fluid and force it through the outlet through rotation
- Can generate very high pressures even at low flow rates
- Great for higher viscosity fluids like heavy oils, asphalt, concrete, etc.
- More complex internally with tighter tolerances
- Common applications include metering, chemical injection, and thick liquid transfer
Specialty Pumps
- Unique designs for specialized duties like:
- Drum/barrel pumps
- Diaphragm pumps
- Peristaltic pumps
- Magnetic drive pumps
- Made for applications like lifting from containers, abrasive/solids handling, gentle sterile pumping, zero-leakage, and more
- Narrower scopes but well-suited for their particular uses
Discuss the fluid properties and system parameters with an engineer to determine whether a centrifugal, positive displacement, or specialty pump is best for your application.
Critical Pump Features for Your Application
While pumps may look similar on the outside, subtle internal differences can vastly affect performance, maintenance, and the suitsability for your application. Here are some key features to examine closely.
Materials of Construction
Pump materials must be compatible with the liquid pumped. Using the wrong materials leads to accelerated wear, corrosion, and pump failure.
- Metallurgy choices like cast iron, stainless steel, alloy steels
- Elastomer choices for o-rings, seals, diaphragms
- Consider liquid properties like viscosity, corrosiveness, temperature, abrasiveness
Bearing Type
Bearings support the shaft and allow smooth rotation under load.
- Ball bearings for high speeds and lower loads
- Roller bearings for heavier loads and lower speeds
- Sleeve/bushing bearings for high contamination resistance
Seal Configuration
Seals prevent leakage around the pump shaft.
- Component seals (PEK) for reliability and lower cost
- Cartridge seals for convenience and quick replacement
- Dual seals for hazardous liquids
- Magnetic drives for zero-leakage of volatiles
Certifications
Certifications show pumps are made for specific applications.
- Explosion proof - for flammable/explosive atmospheres
- Sanitary/hygienic - for food and pharmaceutical
- API 676 - for refinery/pipeline services
Discussing pump features with an engineer ensures you get the right configuration for your specific application parameters and requirements.
Top products in 🔩 Pumps & Accessories
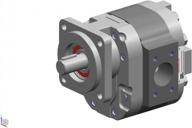
3 Review
Pump Curves and System Design
To properly size and select a pump, it's essential to understand pump performance curves and how the system parameters interact with the pump's capabilities.
What is a Pump Curve?
A pump curve shows the relationship between flow rate, head, efficiency, and power draw for a particular pump model and impeller size.
- Flow rate on x-axis
- Head/pressure on y-axis
- Tracks head, efficiency, and horsepower across flow range
Using Pump Curves for Selection
The system head curve is plotted based on required flow and pressure. This is overlayed on the pump curve to visualize sizing and match.
- Pump must meet head/pressure requirements
- Operating point is intersection of system and pump curve
- Confirms pump selection meets needs
Optimization Opportunities
The shape of the pump curve reveals optimization potential.
- Trim impeller diameter if pump oversized for head
- Increase impeller size if pump undersized
- Ensure operating point falls in best efficiency range
Real World Examples
In one case, a plant was having problems with premature failure of their process pump. Analyzing the curves showed the pump was operating in an end of curve, high-horsepower region due to changes in their system over time. Trimming the impeller diameter shifted the curve left, moving the operating point closer to best efficiency and resolving the issues.
Understanding pump curves unlocks the ability to properly size, troubleshoot, and optimize pumping systems.
Choosing the Right Pump Accessories
Properly selecting accessories and ancillaries for your pump setup ensures smooth operation and helps prevent issues down the road.
Inlet Accessories
Inlet accessories help optimize suction conditions.
- Strainers protect pump from debris ingestion
- Vacuum gauges monitor inlet suction
- Check valves prevent backflow
Outlet Accessories
Outlet accessories help tune discharge conditions.
- Valves provide flow control
- Pressure gauges monitor discharge
- Safety relief valves protect against excessive pressure
Installation Ancillaries
Proper pump mounting ensures stability and allows service.
- Baseplates provide solid foundation and simplify install
- Coupling guards protect against rotating parts
- Isolation valves allow pump removal without draining system
Monitoring Instruments
Instruments provide visibility into pump health.
- Flow meters dial in flow rate
- Vibration sensors catch imbalance issues
- Temperature detectors identify overheating
Choosing the right accessories and ancillaries prevents problems, improves monitoring, and ensures optimal pumping system operation.
How Amazon Prime Improves Your Pumps and Accessories Purchases
Amazon Prime provides a number of benefits that can enhance your experience when purchasing pumps and related accessories online. Here are some of the key advantages Prime provides for fluid handling equipment buyers.
Free Two-Day Shipping
One of the main perks of Amazon Prime is free two-day shipping on millions of eligible items. This means you can get your pumps and accessories delivered right to your door in just two days without having to pay extra for expedited shipping.
This can be extremely valuable if you need a replacement pump or part quickly to minimize downtime. You don't have to pay rush delivery fees to get your order rapidly.
Free Returns
Amazon Prime also makes returns free and easy. If you order a pump or accessories that end up being incorrect or unsuitable for your needs, you can return them for a refund at no extra cost.
This makes it lower risk to order several pump models or accessories to test and evaluate. You can return whatever doesn't work out without hassle.
Access to Exclusive Deals
Prime members get access to exclusive deals and discounts that aren't available to non-members. This includes special pricing on select pumps and accessories that could potentially save you a considerable amount of money.
You can find pumps, strainers, valves and other equipment at discounted prices not advertised to regular Amazon customers.
Overall, an Amazon Prime membership can provide significant advantages and added convenience for purchasing pumps, accessories, parts and related equipment online.
What Are The Most Common Problems Faced By Users Of Pumps And Accessories??
Unfortunately, the search results provided are not relevant to the question about the most common problems faced by users of pumps and accessories. However, based on general knowledge and research, here are some common problems that users of pumps and accessories may face:
What Are Some Common Solutions To The Problems Faced By Pump Users??
Based on the search results, here are some common solutions to the problems faced by pump users: