Intro to Ceramics & Pottery
History of Ceramic Art
Ceramics and pottery have been around for thousands of years, with some of the earliest known ceramic artifacts dating back to 24,000 BCE. Ceramics were developed independently by cultures all over the world, with notable early examples found in East Asia and the Near East. Ceramic technology allowed early civilizations to store and transport water, food, and other goods safely and efficiently. From simple bowls and jars, ceramic art grew into a major form of creative expression in many cultures.
Key Developments
- 24,000 BCE - Earliest known ceramic artifacts from dolomite caves in Czechoslovakia
- 10,000 BCE - Pottery developed in East Asia and the Near East
- 3,000 BCE - Potter's wheel appears in Mesopotamia, allowing symmetrical vessel shapes
- 500 BCE - High-fire pottery glazes developed in China and Greece
- 14th century - Porcelain techniques perfected in China
- 18th century - European porcelain production booms with Meissen technique
Main Types of Ceramic Wares
There are three main categories of pottery and ceramic wares:
Earthenware
Earthenware is pottery fired at lower temperatures, up to 2,000°F. It is porous and not fully vitrified. Common types include terracotta and redware. Used for flower pots, dishes, decorative items.
Stoneware
Stoneware is fired between 2,200 - 2,400°F, resulting in non-porous, vitrified ware. It can hold liquids without leakage. Common types are salt-glazed or slip-decorated stoneware. Used for crockery, jugs, and other utilitarian wares.
Porcelain
Porcelain is fired between 2,400 - 2,550°F and is highly vitrified. It is smooth, white, and translucent. Developed in China, porcelain is valued for artistic expression. Used for figurines, vases, tableware.
Type | Firing Temp | Properties | Uses |
---|---|---|---|
Earthenware | Up to 2,000°F | Porous, low strength | Flower pots, dishes |
Stoneware | 2,200 - 2,400°F | Non-porous, vitrified | Crockery, jugs |
Porcelain | 2,400 - 2,550°F | Translucent, smooth | Figurines, vases |
Ceramic Glazes and Decoration
Glazes and decorative techniques are used to enhance the appearance of finished ceramic wares. Common methods include:
- Glazing - Vitreous coatings applied before final firing
- Slip - Colored liquid clay coatings
- Engobe - Soft clay slurry coatings
- Sgraffito - Surface carved to reveal colored layers beneath
- Mishima - Incised surface patterns filled with colored slip
The variety of possible ceramic glazes and decorations allows for immense artistic creativity. Master potters can produce stunning visual effects in their work.
History of Ceramic Art
Ceramics have been an integral part of human civilization for thousands of years. From prehistoric pottery to ancient Greek vases to delicate porcelain, ceramic art has taken many forms across different cultures and time periods.
Origins of Pottery
- Earliest known pottery dates back over 20,000 years to the Paleolithic period
- Hand-shaped and low-fired vessels created by hunter-gatherer cultures
- Pottery allowed early humans to store, transport, and cook food safely
Ancient Ceramic Cultures
Many ancient civilizations developed rich ceramic traditions and innovative techniques.
China
- Earliest Chinese pottery from 18,000 BCE
- High-fire glazed ceramics by 3rd millennium BCE
- Intricate porcelain wares developed in Tang dynasty
Mesopotamia
- Earliest glazed pottery examples from 4,000 BCE
- Cylinder seals and painted decoration
- Glazing and wheel-throwing techniques spread to Egypt and Greece
Greece and Rome
- Variety of vase and vessel forms with red and black figure painting
- Lifelike Greek figurines and portrait busts
- Glazed and relief ceramics mass-produced in Roman Empire
Ceramics Through the Ages
Ceramic art continued to evolve with the emergence of new techniques and aesthetic styles.
- Persian lusterware ceramics with iridescent metallic glazes
- Intricate Islamic tilework and mosaic murals
- Blue and white porcelain of Ming Dynasty China
- Delftware tin-glazed pottery from the Netherlands
- European porcelain production starting in 18th century
- Art Nouveau, Art Deco, and Mid-Century modern ceramic styles
Today, ceramic arts remain an important form of creative expression and industrial design around the world.
Main Types of Ceramic Wares
Ceramic wares encompass a wide range of products made from clay that has been permanently hardened through high temperature firing. There are three primary categories of ceramic wares, each with their own unique properties and applications.
Earthenware
Earthenware refers to pottery fired at relatively low temperatures, typically between 1,800-2,000°F. The clay remains porous after firing, limiting earthenware's liquid-holding ability but providing a more natural, textured appearance.
- Terracotta plant pots are a common earthenware product, made from red firing clay.
- Redware dishware has an earthy look and often features hand-painted regional designs.
- Earthenware comprises most European Medieval and Colonial American pottery due to lower firing technology.
Top products in 🏺 Ceramics & Pottery
Stoneware
Stoneware is fired at higher temperatures ranging from 2,200-2,400°F which vitrifies the clay into an impermeable, non-porous product.
- Ceramic crockery like jugs, bowls, and food storage containers are often made of stoneware.
- Glazed stoneware creates a smooth, glassy surface that resists staining and damage.
- The brown salt glaze finish of German stoneware beer steins is a classic example of stoneware.
Similar products
Porcelain
Porcelain represents the pinnacle of ceramic development, fired between 2,400-2,550°F for maximum vitrification and density. It is known for its bright white color and delicate, translucent qualities.
- Bone china dinnerware is a type of porcelain prized for its strength and refined appearance.
- Porcelain vases, figurines, and decorative wares require meticulous craftsmanship.
- Electrical insulators are often made of porcelain due to its high resistivity and dielectric strength.
There are no strict divisions between ceramic ware types, and many hybrid ceramics exist. But these three main categories provide a useful framework for understanding ceramic products.
Ceramic Glazes and Decoration Techniques
Glazes and decorative treatments are applied to finished ceramic wares to enhance their appearance and durability. Mastering these techniques is an integral part of ceramic artistry and production.
Glazing
Glazes provide a glassy coating for ceramics that can serve decorative and functional purposes.
- Clear lead glazes allow silhouettes of vessels to remain visible on ancient Greek Amphorae jars.
- Colored glazes like copper red and cobalt blue have been used since 8th century Islamic pottery.
- Commercial glazes for mass production are carefully formulated for reliability and color consistency.
Slips and Engobes
Slips and engobes are fluid clay suspensions applied to ceramics as a coating.
- Red earthenware slips provide background color on black porcelain vases.
- White engobe underglazes block light clay tones on stoneware.
- Colored casting slips are used to tint liquid clay for making ceramics.
Incised and Relief Techniques
Patterns can be formed on clay through incising, carving, or adding relief elements.
- Sgraffito involves scratching through a colored slip to reveal a lower layer.
- Mishima is an inlay method using thin incisions filled with colored slip.
- Ceramic tiles may feature textured relief for aesthetic effect.
Mixed Media Approaches
Ceramic decoration can incorporate other materials.
- Terra sigillata polishing exposes iron particles on the clay surface.
- Raku pottery uses a fast-firing process creating metallic crackled finishes.
- Some porcelain wares feature gilding, enameling, or lacquer decoration.
Endless variations of glazes, slips, carving, and mixed media offer ceramic artists limitless room for creativity and innovation in their works.
Getting Started with Pottery
Pottery is a fun, relaxing hobby that allows you to get creative working with clay. Here are some tips for pottery beginners to help you get started on the right foot.
Choose Your Workspace
Consider your available space when planning your pottery setup:
- A garage, basement, or shed works well for containing messy projects.
- You'll need access to water for mixing clay and cleaning up.
- Make sure the area has adequate ventilation for airing out clay dust.
Obtain Equipment
Basic pottery supplies to have on hand include:
- A potter's wheel for throwing vessels (can be expensive, consider used or starter model).
- Plastic buckets, bowls, and spray bottles for working with clay slip.
- Basic hand tools like loop tools, ribs, cut off wire, fettling knife.
- A kiln or access to one at a local studio (firing clay is essential).
Choose Your Clay
Select clay suited to your project needs:
- Stoneware or porcelain for high-fire wheel throwing and sculpture.
- Earthenware or terracotta clays for handbuilding and low-temp firing.
- Pre-mixed clay is convenient for beginners; buying clay in bulk is economical.
Start Simple
As a beginner, focus on fundamental techniques:
- Practice centering clay on the wheel, then try basic cylinders, bowls, cups, plates.
- Make basic pinch pots, coils pots, and slabs to get a feel for handbuilding.
- Master trimming and cleaning up clay surfaces when leather hard.
Experiment and Refine
As your skills develop, aim to:
- Refine your form—make pieces more symmetrical, uniform, delicate.
- Vary shapes and add decorative elements like textures, handles, feet.
- Try different glazes and finishing techniques like carving, staining, etc.
Be patient with yourself as pottery takes practice. Stay motivated and have fun with the process!
Another interesting products
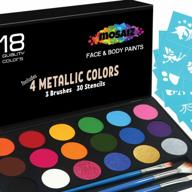
36 Review
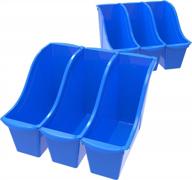
35 Review
Pottery Wheel Basics
The pottery wheel is the primary tool for throwing symmetrical ceramic vessels. Here are some key tips for getting started with wheel throwing.
Prepare the Clay
Knead clay to remove air bubbles and achieve an even, plastic consistency. For throwing, clay should feel soft but not sticky. Let clay sit wrapped in plastic to hydrate before using.
Center the Clay
Start with a softball sized lump. Quickly shape it into a cone and secure clay to wheelhead by gently pressing down while spinning slowly. Stop wheel and compress base of cone with fingers. Repeat centering process until clay is centered.
Open the Clay
With centered clay, use thumbs to bore out a hole in the top. Widen hole steadily with fingers, supporting walls. Open clay until about 4 inches wide for a cylinder or bowl.
Raise the Walls
- Place fingers and apply even pressure on inside wall, slowly raise clay up with pinching motion.
- Repeat raising process gradually. Keep wall thickness even by compressing rim after each pull.
- Tall, thin pieces require slower wheel speed and support inside the vessel.
Shape the Form
When desired height is reached, refine shape with rib tools:
- Compress rim to define lip and shape top opening.
- Use wooden rib to smooth walls and even thickness.
- Metal rib can trim excess clay and refine contours.
Finish the Bottom
Trim excess clay from the bottom with wire tool, then:
- Cup rounded shapes in both hands and compress walls inwards.
- Drag wooden rib across bottom in circles to smooth surface.
- Let vessel stiffen slightly before removing from wheel with wire.
Mastering the pottery wheel takes practice, but following these basics will get you throwing simple forms to start.
Handbuilding Techniques for Pottery
Handbuilding involves shaping ceramic vessels and forms without the use of a pottery wheel. It allows for asymmetrical and unique organic shapes not possible on the wheel.
Pinching
Pinching is likely the oldest and simplest handbuilding technique.
- Pinch the clay between fingers and thumbs to form the desired shape.
- Vessels like basic pinch pots, cups, and vases can be made with this method.
- Adding slip and smoothing with tools refines the surface.
Coiling
Coil building joins long clay coils to construct a form.
- Roll out and cut clay coils, then stack and blend coils together.
- Coils can form entire vessels or be applied decoratively.
- Blending slip between coils and sculpting the surface unifies the texture.
Slab Construction
Slab building uses flat clay planes joined together.
- Roll out clay slabs of consistent thickness using guides.
- Cut and attach slabs using slip and scoring to form shapes.
- Molds can help form curved slab pieces for complex forms.
Sculpting
Freeform sculpting shapes solid blocks of clay by carving.
- Subtractive methods remove clay using tools and fingers.
- Solid forms like figures, vases, bowls can be sculpted.
- Surface textures and patterns can be carved into the clay.
Handbuilding allows potters to be sculptural and creative with their ceramic work. Blending methods like coils over slabs or pinched elements creates unique effects.
Explore The Timeless Beauty Of Salt Glaze Stoneware
Salt glaze stoneware is a beautiful and timeless pottery style that has been around for centuries. Here are some ways to explore and appreciate this unique craft:
Whether you're a collector, a maker, or simply an admirer of pottery, salt glaze stoneware is a beautiful and fascinating craft to explore.
What Are Some Techniques Used To Create Salt Glaze Stoneware?
To create salt glaze stoneware, several techniques are used. Here are some of the common methods employed by potters:
- Salting: The process of adding salt to the kiln is called "salting." Traditionally, multiple saltings were used during firing to achieve the desired effect.
- Sodium Silicate or Sodium Bicarbonate Solution: Before firing, a solution of sodium silicate or sodium bicarbonate is applied to the ware body. This solution helps in the formation of the glaze.
- High Temperature Firing: Salt glaze stoneware is fired at high temperatures, typically around 900°C (1660°F). At this temperature, the salt introduced into the kiln vaporizes and reacts with the silica in the clay body.
- Glaze Formation: The salt vapor combines with the silica and alumina in the clay to form a glassy coating on the surface of the pottery. This glaze is known for its mottled texture, often referred to as "orange peel effect" or "Tiger Skin glaze".
- Addition of Oxides: To enhance the color and appearance of the glaze, potters may add oxides such as manganese oxide, iron oxide, or cobalt oxide.
- Individual Pot Making: Salt glazed pottery is typically made in individual pots by skilled potters. Each piece is carefully crafted and the glaze is not applied evenly, resulting in unique and unpredictable patterns.
- Durability: Salt glaze stoneware is known for its durability and ability to withstand harsh conditions
What Type Of Clay Is Used To Make Salt Glaze Stoneware?
The ideal clay for salt glaze stoneware is a high-silica clay body, such as stoneware or porcelain, with a low shrinkage rate and a strong tolerance to thermal shock. The clay should ideally be richer in silica than normal stoneware, and iron impurities can help produce good salt glazes. Clay that is being used for salt glazing needs to have a high silica content because the sodium oxide fluxes or melts that silica in the clay. Some types of clay, such as ball clay and china clay, are not suitable for salt glaze stoneware.
Can Other Types Of Clay Be Used To Make Salt Glaze Pottery
The ideal clay for salt glaze stoneware is a high-silica clay body, such as stoneware or porcelain, with a low shrinkage rate and a strong tolerance to thermal shock. However, other types of clay can also be used to make salt glaze pottery, but they may not produce the same results as high-silica clay. For example, some potters use earthenware clay for salt glaze pottery, but the glaze may not be as durable as that produced by stoneware or porcelain. The type of clay used for salt glaze pottery needs to have a high silica content because the sodium oxide fluxes or melts that silica in the clay. Some types of clay, such as ball clay and china clay, are not suitable for salt glaze stoneware. The clay used for salt glaze pottery needs to be able to withstand high temperatures and thermal shock, as well as have a low shrinkage rate to prevent cracking during firing.