Removing Paint and Rust from Metal Surfaces
Removing old paint and rust from metal surfaces like iron, steel, and aluminum is an important part of maintenance and restoration projects. Proper paint and rust removal allows you to reveal the bare metal underneath so that you can repaint or treat the surface. There are several methods and tools available for effective paint and rust removal depending on the specifics of your project.
Similar products
Chemical Paint Removers
Chemical paint stripping products provide a convenient way to remove multiple layers of paint. They come in both liquid and gel forms. The active ingredient in most chemical strippers is methylene chloride, which works to soften and blister paint so that it can be more easily scraped off. Here are some tips for using chemical paint removers:
- Cover any nearby surfaces you don't want to strip since removers can splash and spill over
- Apply a thick, even coat of the remover and let it sit for 15-30 minutes
- Use a plastic scraper to scrape off the softened paint
- Repeat for any remaining paint layers
- Rinse thoroughly with water when finished
Another interesting products
Abrasive Brushes
Abrasive brushes use gritty bristles to literally scrub away paint layers and rust. They come in various sizes and bristle types. Here are some examples:
- Wire brushes have twisted or crimped steel wire bristles that are good for removing rust and thick paint
- Stainless steel brushes won't scratch the metal underneath as much as standard wire brushes
- Brass brushes are even more gentle than steel
When using abrasive brushes:
- Select a brush appropriate for your surface - more delicate surfaces require softer brushes
- Rub the brush back and forth using moderate pressure
- Clean out the brush bristles frequently to remove paint debris
- Thoroughly clean and dry the surface when finished
Top products in 🧼 Abrasive Brushes
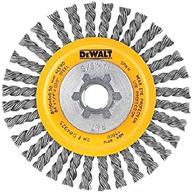
10 Review
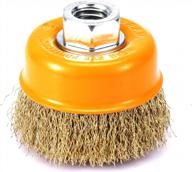
12 Review
Sandpaper and Sanding Tools
For small paint removal jobs, you can use sandpaper and sanding sponges. Progress through grits from coarse to fine. Pay attention not to remove too much base material. Belt sanders, palm sanders, and other power sanders allow you to sand larger areas more quickly. Be aware of potential damage from over-sanding or remaining swirl marks.
Sandblasting uses compressed air to shoot abrasive media at high velocity to strip surfaces. It removes paint and rust quickly but should only be done by professionals due to equipment costs and safety risks.
Rust Removers
Chemical rust removers work by converting rust into a water soluble compound that can be rinsed away. They are available in liquid, gel, and spray forms. For best results:
- Scuff up the surface with abrasives first to help the solution penetrate
- Apply a thick coat of the rust remover and allow it to sit for 10-30 minutes
- Scrub with stiff brushes or abrasive pads
- Rinse thoroughly when the rust is gone
With any rust removal method, make sure to wear appropriate safety gear and work in a well-ventilated area. Treating the now bare metal surface with a rust preventative coating is also advised to stop new rust from forming.
Achieving a Polished Finish on Wood
Applying a polished finish to wood brings out its natural beauty and gives it an attractive sheen. Polished finishes enhance the grain patterns in wood and provide some protection from wear and light damage. The process involves sanding the wood to ensure a smooth surface and then applying a clear finish, like polyurethane or varnish, to seal and polish the wood.
Sanding the Wood
Proper sanding is crucial for getting a flawlessly smooth finish. It removes any rough spots, scratches, dust nibs, or other blemishes from the wood surface. Work through progressively finer grits of sandpaper:
- Start with 80-100 grit to smooth the surface
- Progress to 150 grit for minor scratches
- Finish with 220-320 grit to erase sanding marks from previous grits
On turned wood objects, wet sanding helps achieve an extra smooth finish. Dip the sandpaper in water or mineral spirits as you sand. The fluid lubricates the sanding process and clogs the pores of the wood slightly to create a smooth, closed grain finish when dry.
Applying a Seal Coat
Before the final polish layers, it's a good idea to apply a seal coat like sanding sealer or dewaxed shellac. This seals the wood pores and provides a stable base for the following finish coats. Simply use a clean rag or brush to apply a thin layer, then let it dry fully.
Using a Polishing Oil
Oils like tung oil and Danish oil contain varnish resins that cure and harden in the wood to build a protective film. Apply with a clean rag following the product directions. Let the oil fully cure, usually 1-3 days. Smooth any raised grain with a fine sanding pad or 0000 steel wool before adding more coats. 3-5 thin coats are recommended for best results.
Applying Varnish
Varnish provides a clear, durable polished finish. Both oil-based and water-based varnish formulas work well. Follow these tips when varnishing:
- Use a high quality natural bristle or foam brush
- Maintain a wet edge as you brush on the varnish to avoid lap marks
- Sand lightly with 400 grit sandpaper between coats
- Apply at least 3 coats for best protection and sheen
Using Polyurethane
Oil-based polyurethane provides a very hard, durable polished finish. Water-based polyurethane is easier to apply and clean up but less protective. Follow the same application tips as for varnish. Pay careful attention to drying times between coats.
Applying Wax
For an easy buffed shine, wax makes a great final step. Use a soft cloth to apply a thin, even coat of a high quality paste wax. Let the wax dry completely then buff it out with a clean cloth. Multiple wax layers can build an even deeper, wet-look shine.
Achieving a mirror-like polished finish on wood takes time and effort but is very rewarding. The proper sanding techniques and finishing products result in a smooth, protective shine that brings out the best in your woodworking projects.
Cleaning Grease and Grime from Concrete Floors
Grease, oil, dirt, and grime can quickly build up on concrete floors, leaving them looking dirty and neglected. Regular cleaning is essential for garages, warehouses, commercial kitchens, and any facility with concrete flooring. The porous nature of concrete allows spills to soak in deeply and stain if left untreated. However, the right cleaning solutions and techniques can effectively remove built-up grease and restore the look of concrete.
Cleaning Solutions
Specialized concrete degreasers work best for removing stubborn oil and grease stains from concrete. Look for alkaline-based cleaners that contain surfactants, emulsifiers, and/or solvents to cut through grease. Here are some common concrete degreasing products:
- Sodium Carbonate - Dissolves grease and oil
- Sodium Metasilicate - Loosens dried and baked-on grease
- Sodium Hydroxide - Also called lye, dissolves fatty acids in grease
- Solvents - Help lift oil-based stains
Cleaning Methods
For light grease buildup, mopping the concrete with a heavy duty alkaline cleaner diluted with water may suffice. Scrub stains with a stiff bristle brush. Rinse thoroughly and repeat as needed.
For heavy grease and oil stains:
- Apply a concentrated layer of degreaser directly onto the stain
- Let sit for 5-10 minutes
- Scrub with a stiff bristle brush, floor buffer, or pressure washer
- Rinse thoroughly with hot water
Proper safety gear such as gloves, eye protection, and boots should be worn. Promptly clean up and dispose of used degreasing solutions.
Prevention
To minimize buildup of concrete floor grease and stains:
- Place absorbent floor mats at entrances
- Clean spills immediately
- Use a concrete sealer/hardener
- Implement a regular cleaning schedule
With the right techniques and products, concrete floors can be restored to a clean, grease-free condition.
Smoothing Rough Welds on Metal Joints
Welded metal fabrications often require smoothing out to achieve a uniform, attractive appearance. Rough weld seams create stress concentrations and weak points in the assembly. Removing sharp edges also eliminates potential safety hazards. Here are some effective methods for smoothing weld seams on metal components.
Grinding
Handheld angle grinders with grinding wheels are commonly used to smooth welds. This abrasive method removes material to even out the weld profile with the base material. Use care to avoid overgrinding, which can weaken the weld joint. Tips for grinding welds:
- Select the appropriate wheel type and grit size for the material being smoothed
- Use the correct wheel for the grinder's RPM rating
- Position the grinder to avoid gouging into the base material
- Make smooth, controlled passes over the length of the weld
Flap Discs
Flap discs attach to angle grinders like grinding wheels but use overlapping abrasive flaps instead of solid abrasive. The flaps easily conform to curves and contours. This makes flap discs ideal for smoothing weld transitions on tubing, rounded edges, and irregular profiles.
Filing/Sanding
Hand files allow controlled removal of weld metal. Common file types such as flat, half-round, and triangular match various joint configurations. Use short, even strokes and frequently clean the file. Follow up with progressively finer grit sandpaper for a polished finish.
Abrasive Flap Wheels
Abrasive flap wheels consist of abrasive cloth applied to a rotating mandrel. On bench grinders or other rotating tools, flap wheels smooth welds quickly with a light touch. The flexible flaps easily fit corners and odd angles.
Die Grinders
Air or electric powered die grinders use small diameter grinding wheels and cutters at high RPM for detailed grinding. The narrow wheels can smooth fillet welds and reach tight spots. Take care not to grind too deeply or rapidly.
For quality, lasting welded structures, take the time to properly smooth welds. Blend them evenly into the surrounding base material for a less visible, attractive finish.
Deburring and Finishing 3D Printed Parts
One of the advantages of 3D printing is the ability to produce complex geometries that would be difficult or impossible with traditional manufacturing methods. However, the layered nature of 3D printed parts creates small ridges and uneven surfaces that require post-processing to smooth out.
Removing Support Material
Many 3D prints use dissolvable support material during the build process to allow overhangs and undercuts. After printing, this support material must be removed to reveal the finished part's full details. Typical methods include:
- Dissolving in water or alkalines - Works well for PVA and HIPS supports
- Breaking away supports by hand - Effective for brittle SRP and PLA supports
- Cutting away larger supports with flush cutters
Sanding
Light sanding removes any remaining support nubs and smoothes layer lines. Start with a medium (150-220 grit) sandpaper and wet sanding to keep particles under control. Be careful not to sand away fine features. For detailed areas, fingertip sanding or small hobby files work well.
Filleting Sharp Corners
Internal corners and edges on 3D prints can be fragile stress points. A quick pass with a round hobby file or small drill bit will radius these edges for improved durability.
Vapor Smoothing
Exposing the plastic surface to vaporized solvents will melt the outer layer slightly for a smooth, glossy finish. This is effective on ABS and PLA prints but handling safety is critical due to toxic solvents.
Tumbling
A rock tumbler can deburr and polish 3D printed parts similar to small metal components. Use a wear-resistant media like ceramic pellets to gently erode surface imperfections over time.
Priming and Painting
Priming and painting the part can hide layer lines along with providing color and protection. Sanding provides "tooth" for paint adhesion. Properly preparing the surface avoids chipping or peeling later on.
Well-finished 3D printed parts blend the advantages of additive manufacturing with a refined, polished look. Post-processing removes rough edges and layer steps to maximize a part's appearance and durability.
Cleaning Brick, Stone, and Other Masonry
Over time, exterior masonry accumulates dirt, grime, mold, and stains from weather, pollution, and other environmental factors. Keeping brick, natural stone, concrete, and mortar clean not only improves appearance, but also extends the life of the masonry.
Pressure Washing
Power washing with a commercial pressure washer (1500-4000 psi) is effective for removing loose debris and surface dirt from masonry. Use the fan spray tip and keep the nozzle at least 1 foot away to avoid damaging the masonry face.
Chemical Masonry Cleaners
Alkaline-based masonry cleaners help dissolve and remove oily dirt, paint, and stains. Options include:
- Sodium Hydroxide - Dissolves oils and greasy residues
- Sodium Hypochlorite - Bleaches and disinfects
- Hydrogen Peroxide - Non-toxic oxidizing cleaner
Apply cleaners using a masonry brush or low pressure sprayer. Let sit for 5-10 minutes before rinsing thoroughly with water.
Mold and Mildew Removers
Mold and mildew can grow on any damp, shaded masonry surface. Using chlorine bleach or oxygen bleach cleaners will both remove stains and kill spores. For less damage to plants, hydrogen peroxide products work too.
Rust Stain Removers
Rust stains from metal flashings, railings, pipes, etc. can bleed onto surrounding masonry. Oxalic acid effectively removes these rust marks without altering the stone or brick.
Safety Tips
- Test cleaners on an inconspicuous spot first
- Read and follow all product instructions
- Wear protective eyewear, gloves, clothing
- Protect plants and grass from splash damage
Regular masonry cleaning maintains aesthetic appeal while also extending the service life of the wall. Careful application of the proper cleaners gets rid of dirt, stains, and discoloration.
Cup Type Brush
A cup type brush is an abrasive tool that is used for cleaning, deburring, and polishing flat or curved surfaces. The brush is constructed by attaching wire bristles or filaments to a cup-shaped base. Cup brushes are available in different duty levels and fill materials to suit a wide variety of tasks. They are generally used for removal of scale, rust, and paint, as well as for deburring and polishing. Cup brushes are available in different sizes and with different shank or arbor hole options. They are commonly used on large areas to remove rust, paint, and scale. Cup brushes are also suitable for deburring, weld cleaning, and surface preparation.
What Are The Different Types Of Cup Brushes Available??
There are different types of cup brushes available, each designed for specific applications. Here are some of the types of cup brushes:
- Standard Cup Brushes: These are designed for removing light deposits of scale, paint, rust, and small burrs. They are available in carbon steel, stainless steel, brass, and nylon. Standard models come with a 1⁄4” shank or 1⁄2” arbor hole. The approximate trim length is 3⁄4”. The recommended maximum safe free speed ranges from 8,000 rpm to 10,500 rpm. Diameter options include 13⁄4”, 2′′, and 2 3⁄4”.
- Minigrinder Cup Brushes: These are designed for higher speed rotation in a high-speed angle grinder. They are suitable for deburring, weld cleaning, paint and rust removal, and surface preparation. They are available standard with carbon steel, stainless steel, brass, or bronze wire in both crimped and twisted.
- Knotted Cup Brushes: These are designed for heavy-duty applications such as weld cleaning, heavy scale removal, and surface preparation. They are available in carbon steel, stainless steel, and brass. They come with a 5/8”-11 arbor hole and are available in diameters ranging from 2 3⁄4” to 6”.
- Stringer Bead Cup Brushes: These are designed for cleaning weld beads, corners, and other hard-to-reach areas. They are available in carbon steel, stainless steel, and brass. They come with a 5/8”-11 arbor hole and are available in diameters ranging from 2 3⁄4” to 6”.
- Crimped Wire Cup Brushes: These are designed for light to medium-duty applications such as cleaning and polishing. They are available in carbon steel, stainless steel, and brass. They come with a 5/8”-11 arbor hole and are available in diameters ranging from 2 3⁄4” to 6”.
- Abrasive Nylon Cup Brushes: These are designed for light deburring, edge blending, and surface finishing. They are available in silicon carbide, aluminum oxide, and ceramic abrasive filaments. They come with a 5/8”-11 arbor hole and are available in diameters ranging from 2 3⁄4” to 6”.
- Flap Cup Brushes: These are designed for blending, deburring, and finishing flat or contoured surfaces. They are available in aluminum oxide and zirconia abrasive flaps. They come with a 5/8”-11 arbor hole and are available in diameters ranging from 2 3⁄4” to 6”.